Redesigning the Supply Chain of Alenia Aeronautica
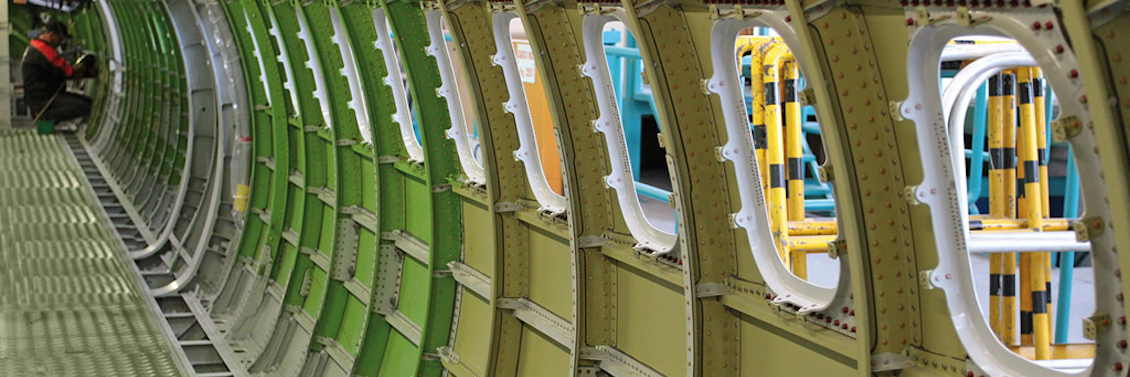
Source: Alenia Aeronautica
The focus on production line requirements, and therefore on the end product, generates the main mission of Supply Chain redesign.
To put into practice the expertise of production line operators and the knowledge gained from partner vendors pre-selected after careful assessments to verify their industrial capabilities and skills, production performance, competitiveness and financial standing, and convert them into excellency results to act as the mainstay of production. These assumptions are at the basis of the pilot project for Supply Chain redesign concerning machine-worked parts of the ATR programme. The starting point is the rationalisation of machined part supplies assembled on section 11 assembly line (cockpit). The project implies the breakdown of mechanical parts into four Work Packages in line with the four assembly macro-areas (bulkhead, glass, upper lobe, lower lobe).Within each Work Package the parts are arranged in as many kits as the assembly stations to be fed.We have selected four vendors to supply a Work Package each, thus avoiding an excessive segmentation of the vendor base.
According to the project, the selected vendors will be responsible for purchasing materials and assembling subgroups; adjusting the basic specifications for the introduction of the parts kits; make planning changes by introducing "pull" logics; defining a takt-time for station infeed synchronisation and parts storage process modification to enable direct station infeed by means of racks. The approach used for section 11 was also applied to the assembly lines of section 15 and of the entire fuselage with the purpose of distributing volumes across partner vendors (“large factories”) that also own the installations required to make surface treatments, in order to streamline logistic production flows. The rationalization of mechanical part supplies have also affected the stabiliser/elevator integration and rudder assembly lines (these are assembled by two vendors). The project is already completed as far as the entire rear fuselage segment is concerned (joint section 16 and 18).
The project progresses by transparent milestones/toll-gates, based on the maximum accountability of all corporate functions. Vendors are selected according to technical/economic assessment matrices, taking also into account the performances had with us and with other Finmeccanica group companies.
The rationalisation of machined part supplies requires the necessary risk mitigation actions to remove any disturbance to production line infeed. In order to manage the transition from partner vendor start-up to their full-rate production as the sole source of parts,we will need to verify the progress status by means of dedicated assessment, performed together with the vendors themselves and with the departments involved.
Massimo Esposito
Procurement & Supply Chain
Supply Chain Re-Design