ThyssenKrupp selected to enhance urban mobility in Italy
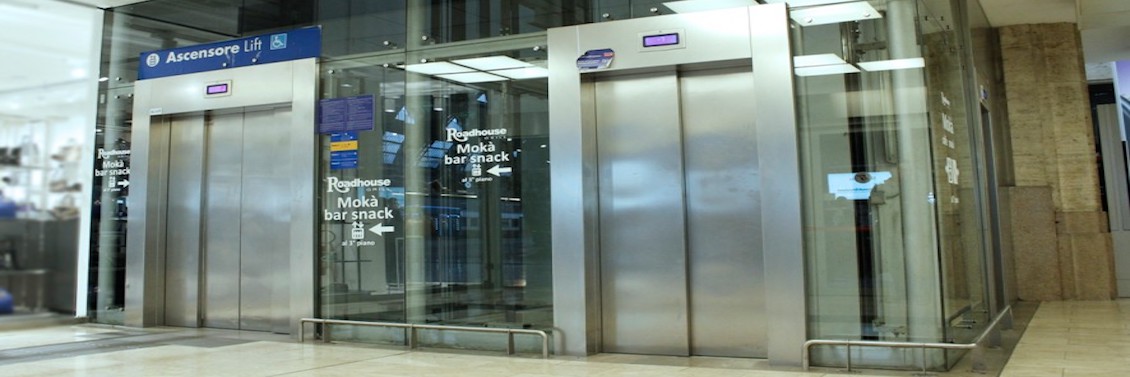
News from our Clients: Thyssenkrupp
ThyssenKrupp has won tenders for the maintenance of over 500 elevators and escalators in the metro stations of Milan and Naples.
ThyssenKrupp celebrates its latest success in urban mobility: the company has won contracts to provide maintenance services for 585 mobility systems in Milan and Naples’ metro stations. Of these, 352 systems (237 elevators, 115 escalators) are spread across of Milan’s 60 metro stations, and 233 systems (83 elevators, 150 escalators) extend over 23 stations in Naples. Combined, the contracts are worth approximately €9 million.
Luigi Maggioni, Managing Director of Thyssenkrupp Elevator Italia stated: “As city populations continue to rise, passenger crowding at metro station junctions and at peak hours has become a major issue of concern, making efficient mobility of people inside metro stations just as important as their mobility between them.”
He added, “We want to address the challenges of urbanization together with our customers and are very proud that Azienda Trasporti Milanesi (ATM) and Azienda Napoletana Mobilita (ANM) have entrusted us with the maintenance of their systems. Every day, 1.2 million commuters transit though these two metro networks, and our goal is to ensure a safe and comfortable journey for each and every one of them.”
Thyssenkrupp has an excellent reputation in the urban mobility industry, as proven by significant tenders recently awarded to the company in Italy. These include a contract to supply and install 88 escalators and 53 elevators, and provide Agenzia del trasporto autoferrotranviario del Comune di Roma (ATAC) with maintenance services at all 30 stations of the metro Line C in Rome, the longest urban underground railway line in Italy with a length of 25km and carrying over 24,000 passengers per hour.
The company is also responsible for providing maintenance services at numerous other railway facilities, including large stations such as Rome Ostiense, Milan Central Station, Turin Porta Nuova, Genova Porta Principe, and others.
Omar Riva, Sales Manager at Thyssenkrupp Elevator Italia, said: “We are able to guarantee time-saving interventions by solving malfunctions within 15 minutes of our arrival on site, which translates to more than 98% system efficiency. These results are thanks to our highly qualified technicians who have over 3,700 hours in operational training and over 2,000 hours in safety training, besides the support provided by our International Technical Services, delivering support for mobility systems of any brand or model. Together with our customer care centers, we are capable of providing 24/7 support, aiming to have mobility equipment always running as it should.”
As a part of its efforts to improve the efficiency of urban mobility systems, Thyssenkrupp introduced MAX, a cutting-edge predictive maintenance system that connects all elevator systems to the cloud with the aim of foreseeing possible malfunctions before they actually happen. MAX is enabled by a highly advanced algorithm designed in collaboration with Microsoft, and is currently being implemented in the US, Spain and Germany; it will be available in Italy in the near future.
Tags: ThyssenKrupp