New Loading Systems with Artificial Vision
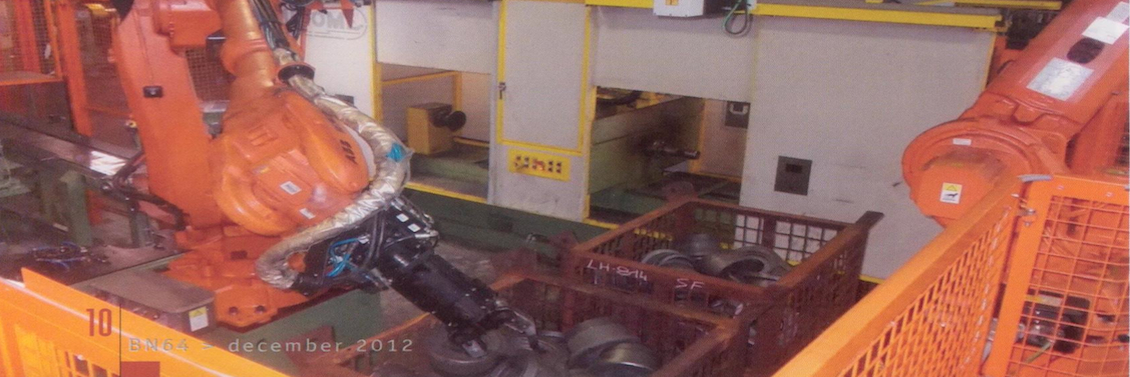
Source: Berco News 64 > December 2012
Industrial automation, based on anthropomorphic robots, was introduced with the aim of freeing operators from more physical, lower value-added tasks.
Now, in the world of automation, a new frontier is emerging, that of anthropomorphic robots controlled not simply by handling software but by intelligent programs that interpret images captured by cameras — in other words, artificial vision systems.
This new technology has been made possible — and applicable at an industrial level — by the ever more dynamic miniaturization of photo-video viewing systems and their expansion into the consumer market, with a consequent reduction in costs.
Thus, after years of experiments and laboratory testing, this technology is now beginning to be applied on an industrial scale.
As a consequence of this, two roller welding cells with artificial vision loading systems have been installed in Berco's Copparo factory. The roller halves are thus taken from the container by an anthropomorphic robot, which receives instructions from a three-dimensional vision system developed by SIR of Modena. The vision system, operated by second anthropomorphic robot by means of a laser-scanner, scans the container, processes the image, compares the result to the mathematical model of the half-roller currently in production and identifies the most easily removable half-rollers. The handling robot sets its target in this way and then moves the half-roller from the container to an intermediate point, where it is analyzed again by a second vision system — this time two-dimensional - to recognize the position of its edge (edge detection). The loading robot now has all the information it needs to handle the item correctly, and can proceed with loading the welding machine.
The same robot can also supply the finishing machine downstream of the welding cell.
The new thing about this application is that the system is able to analyze items stacked randomly in a container, and not just those arranged on a horizontal surface, as in the more common applications. This makes the set-up procedure more complex, and SIR and Berco are working continuously to make improvement in this area. The set-up/optimization activity regards both the calculation algorithms for the main software and the mechanical handling equipment, which has to handle all the items passing through the cell with a single gripper, in order to avoid continuous tooling operations. The installation of these handling/welding cells upstream of finishing machines makes it possible to keep both production lead times and inter-operational buffers low. Once optimized, fully robotic handling can considerably reduce the problems related to the manual handling of loads. The possible prospects of this approach are clear to see and can lead to improvements in all the component handling operations which, generally, are currently performed by the machine operator.
It can also lead to a higher level of training for the operators, who, once relieved of these tasks, can become more involved in process/system control activities.
Nicola Antolini
Head of Rollers Area
Tags: ThyssenKrupp, Berco