Track link processing at Berco Shangai
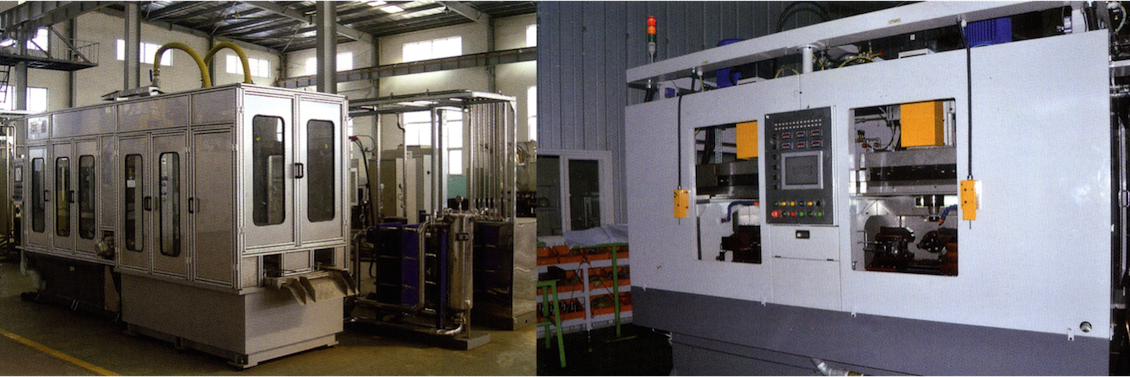
Source: Berco News 64 > December 2012
The main market for medium size excavators (from 14 to 40 tons) is now the Chinese one.
In 2011 a production peak of about 180,000 machines was reached, a substantial percentage of the world production figure. In order to win a greater volume of this section of the market, Berco is investing in the localization of components. The main competitive advantages of localization are the elimination of customs duties, reduced lead time and greater cost stability, in a macroeconomic scenario characterized by sharply fluctuating currency exchange rates.
Two years have gone by since the production of pins and bushings for excavator track chains began in the then newly opened Shanghai factory. Now that the production has consolidated, the time has finally come for the localization of track link processing.
Berco approaches these localization processes in such a way as to guarantee the outstanding quality of its products and compliance with specifications, regardless of where the manufacturing takes place. One would imagine that for a company like Berco, that
produces 8 millions track links every year, the localization of track link processing would be straightforward, but this is not the case. In fact, this is the first time that these components are being produced out of our Italian factories. At this stage, the localization doesn't involve just the processing but also the procurement of the forged parts from local suppliers, until such a time as market volumes allow us to set up our own forging. Thus, a number of actions have been taken in advance to certify the suppliers of both the raw materials and the forging, actions which have involved not only the forging and processing of Chinese steel in Italy, but also the processing of links forged in China on lines in Copparo. These trials and subsequent tests have had positive results, thus allowing us to proceed with the localization of the machining and heat treatment processes in the Shanghai factory. To prepare itself in the best possible way for this challenge, Berco Shanghai has organized specific training courses for some of its engineers at the Copparo factory, to familiarize them with the problems related to the machining and heat treatment of the links.
Just as in the Italian factories, the track links will be produced on dedicated machines that carry outmilling of the shoe mounting and link rail faces the quenching and tempering and, finally, the boring and drilling. A further machine performs the nut seat machining on track links requiring this process.
This work is due to start at the beginning of the New Year, after the setting up of the lines with the help of Italian engineers.
The pitch range covered goes from 190 mm to 228.6 mm, allowing the processing of track links for excavators ranging from 18 to 50 tons.
In this initial stage the production capacity will be 400 tracks, which will double in a second planned stage.
Andrea Minguzzi
Operations Manager
Tags: ThyssenKrupp, Berco